Exploring the Significance of Die Casting Mold Companies in Metal Fabrication
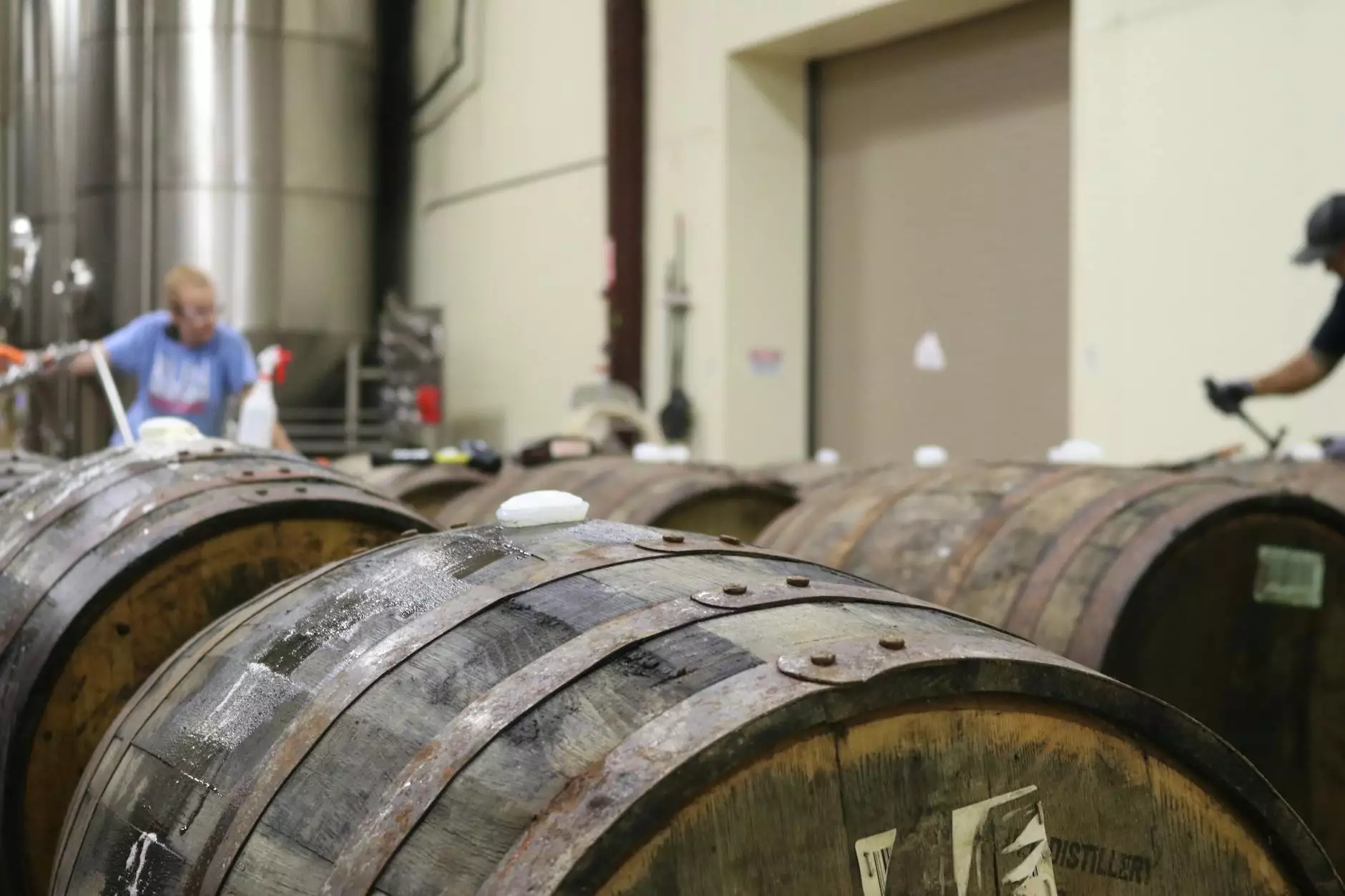
In today's fast-paced industrial landscape, die casting mold companies play a crucial role in the manufacturing process. These companies are not only responsible for creating molds used in the die casting process but also contribute significantly to the overall success of various sectors including automotive, aerospace, and electronics. This comprehensive guide delves into the different aspects of die casting mold companies, showcasing their importance in the realm of metal fabrication.
What is Die Casting?
Die casting is a metal casting process that involves forcing molten metal under high pressure into a mold cavity. The process is highly efficient, enabling the production of complex shapes with excellent dimensional accuracy and surface finish. The molds used in this application are typically made from high-strength materials, designed to withstand the repeated stresses of the casting process.
The Role of Die Casting Mold Companies
Die casting mold companies specialize in designing and manufacturing molds that are used in die casting processes. Their expertise is crucial for several reasons:
- Precision Engineering: Molds are engineered with precision to ensure that the final product meets the exact specifications required by clients.
- Material Selection: These companies choose materials that can endure high pressure and temperature, enhancing durability and performance.
- Cost Efficiency: By creating effective molds, die casting mold companies help reduce manufacturing costs and improve production rates.
- Custom Solutions: Many companies offer customized solutions to meet the unique needs of different industries, ensuring flexibility and adaptability in manufacturing processes.
Industries Benefiting from Die Casting Mold Companies
The impact of die casting mold companies is evident across various industries. Here are some of the key sectors that heavily rely on their services:
1. Automotive Industry
The automotive sector is one of the largest consumers of die casting services. From engine blocks to transmission cases, die casting molds are used extensively for producing lightweight yet durable components. Using die casting, manufacturers can meet the stringent regulations for fuel efficiency and emissions while also achieving high performance and safety standards.
2. Aerospace Industry
Just like the automotive industry, the aerospace sector demands parts that are both strong and lightweight. Die casting mold companies provide the aerospace industry with high-precision molds that produce complex geometries needed for aircraft components. This not only enhances the structural integrity of the aircraft but also contributes to fuel efficiency and overall performance.
3. Electronics Industry
In the electronics field, die casting molds are crucial for manufacturing housings and connectors that require precise specifications. The ability to produce intricate designs at a low cost while maintaining quality makes die casting an attractive option for electronic manufacturers.
4. Consumer Goods
Various consumer products, including appliances and household items, also rely on die casting technologies. The economic advantages and design flexibility provided by die casting mold companies make it an ideal choice for producing a wide variety of consumer goods.
Choosing the Right Die Casting Mold Company
For businesses looking to partner with a die casting mold company, several factors should be considered to ensure a strong collaboration:
- Experience: Look for a company with a proven track record in die casting and the specific industry related to your needs.
- Technology: Ensure that the company utilizes the latest technologies in mold design and manufacturing to guarantee high-quality results.
- Customer Support: A good die casting mold company provides excellent customer support, guiding you through every step of the process, from design to production and beyond.
- Quality Assurance: The presence of quality control measures is essential in maintaining the integrity and precision of the molds.
Best Practices in Die Casting Mold Design
Effective mold design is paramount for the success of the die casting process. Here are some best practices to consider:
1. Design for Manufacturability
Ensuring that the mold design is practical for manufacturing is essential. This involves taking into account the capabilities of the die casting process, including draft angles, wall thickness, and mold flow paths.
2. Optimize Cooling Systems
Efficient cooling within the molds is critical for achieving uniform solidification and reducing cycle times. Designing effective cooling channels can significantly enhance productivity and part quality.
3. Material Selection
The choice of material for the mold should consider factors such as thermal conductivity, wear resistance, and cost. Materials like tool steel or aluminum alloys are often used due to their favorable properties.
4. Regular Maintenance
Regular maintenance of die casting molds is essential to prolong their lifespan and ensure consistent quality. This includes cleaning, inspecting for wear and tear, and making necessary adjustments.
Conclusion: The Future of Die Casting Mold Companies
As industries continue to evolve, the significance of die casting mold companies in metal fabrication remains undeniable. With advancements in technology, these companies continue to innovate, ensuring that they meet the changing demands of their clients. By understanding the importance of die casting and collaborating with the right suppliers, businesses can effectively harness the benefits of this efficient manufacturing process.
In summary, die casting not only streamlines production but also fosters creativity in product design, making it an essential component of modern manufacturing approaches. Whether you are an established corporation or a startup, leveraging the expertise of die casting mold companies can propel your business towards success.