Understanding Concrete Batching Plants: The Backbone of Modern Construction
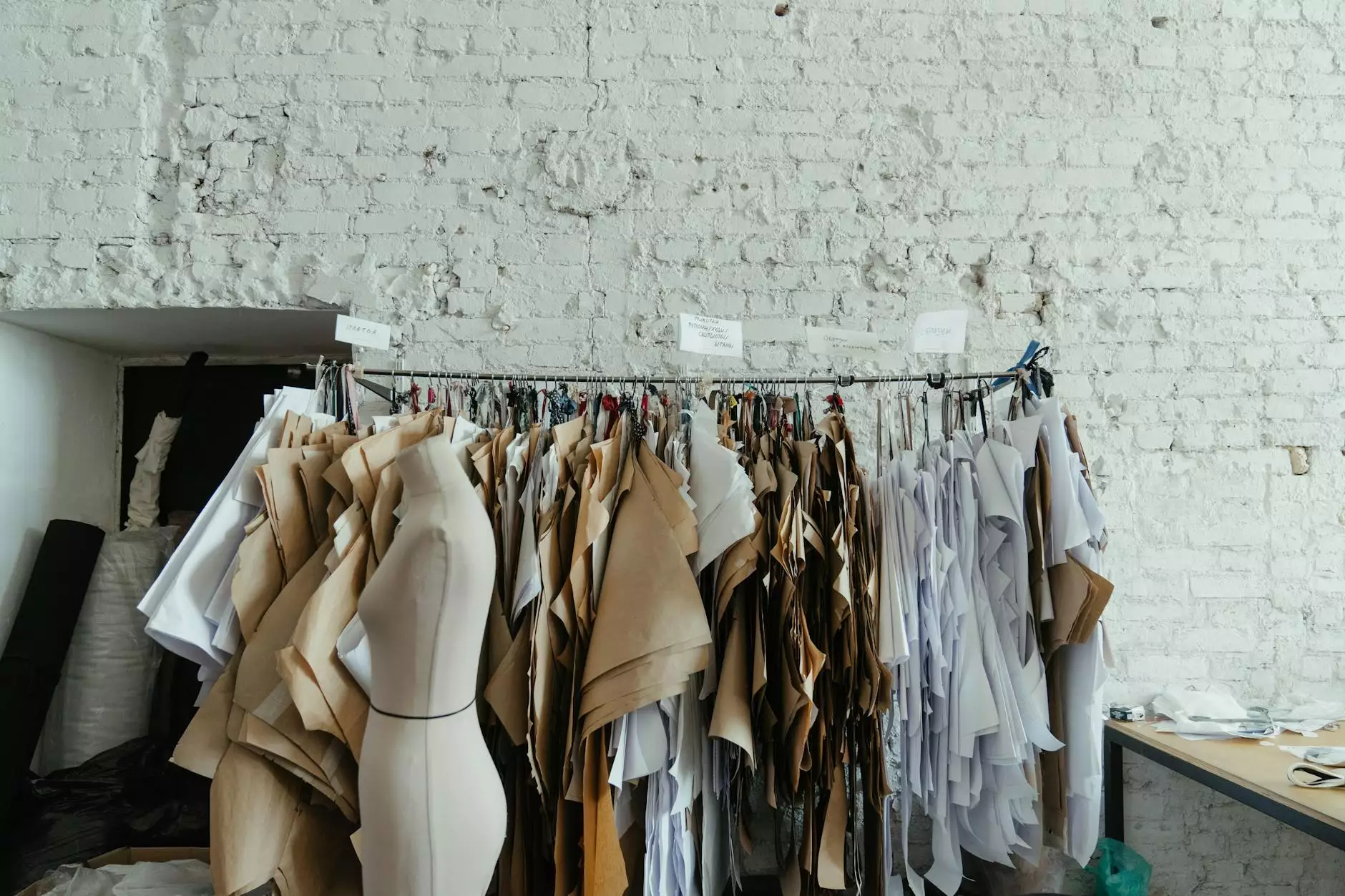
Concrete batching plants are essential components in the construction industry, facilitating the large-scale production of concrete—a material that has become the cornerstone of modern infrastructure. As cities expand and renovation projects intensify, the demand for high-quality concrete is unparalleled. This article delves into the workings, advantages, and types of concrete batching plants, showcasing their pivotal role in the construction sector.
The Importance of Concrete Batching Plants
Concrete batching plants play a vital role in ensuring that construction projects progress smoothly. By producing concrete in large volumes, they help meet the growing demands of both urban and rural development. Without these plants, the construction industry would struggle to supply the necessary materials within time constraints. Here are some key reasons why concrete batching plants are essential:
- Efficiency: Batching plants streamline the concrete production process, allowing construction companies to save both time and labor costs.
- Quality Control: These facilities have the capability to maintain stringent quality standards, ensuring uniformity and durability of concrete mixes.
- Scalability: Batching plants cater to projects of various sizes, from small residential jobs to large commercial undertakings.
- Environmental Benefits: Modern batching plants incorporate eco-friendly practices, reducing waste and utilizing recycled materials.
How Concrete Batching Plants Work
The operation of a concrete batching plant revolves around the accurate measurement and mixing of raw materials, which typically includes cement, water, aggregates, and admixtures. Here's a breakdown of the typical workflow in a batching plant:
1. Raw Material Preparation
The first step in the concrete production process involves preparing the raw materials. Aggregates are sourced, cleaned, and stored in separate bins to prevent contamination.
2. Weighing and Batching
Once the materials are prepared, they are weighed according to the specific recipe required for the concrete mix. Accurate weighing is crucial to ensure the desired strength and consistency of the final product.
3. Mixing
After the materials are batched, they are mixed in a concrete mixer. Depending on the specific plant type, the mixer can be a drum mixer, pan mixer, or twin-shaft mixer. These mixers ensure a homogeneous mixture of all components.
4. Dispatching
After mixing, the concrete is either loaded into delivery trucks or stored in silos, ready for use at construction sites. Quick dispatch times can significantly increase the productivity of construction projects.
Types of Concrete Batching Plants
Concrete batching plants can vary based on their operational setup and the requirements of specific projects. The three main types of batching plants include:
1. Stationary Concrete Batching Plants
Stationary plants are permanently installed at a specific location. They are ideal for large projects that require a consistent and long-term supply of concrete. Their robust construction allows them to handle high capacities efficiently.
2. Mobile Concrete Batching Plants
Mobile batching plants offer flexibility and portability. They can be easily transported to different job sites, which is particularly beneficial for projects that require varying amounts of concrete. This type of plant is perfect for smaller-scale operations and remote locations.
3. Compact Concrete Batching Plants
Compact plants are designed for efficiency in space utilization without sacrificing performance. They are excellent for urban settings where real estate is premium, and they can be set up quickly for immediate use.
Advantages of Using Concrete Batching Plants
Investing in a concrete batching plant comes with numerous advantages:
- Cost-Effectiveness: By producing concrete on-site or in bulk, companies can reduce costs associated with transporting materials.
- Reduced Lead Times: With quick and efficient production, projects can meet tight deadlines.
- Customizable Mixes: Plants allow for tailored concrete recipes, enabling companies to meet specific project requirements.
- Labor Savings: Automated processes reduce the need for manual labor, minimizing potential human error.
Key Components of Concrete Batching Plants
To function effectively, a typical concrete batching plant consists of several critical components:
1. Aggregate Bins
These bins store different sizes of aggregates. They are designed to prevent segregation and contamination of materials.
2. Weighing Scale
Accurate weighing scales ensure that the right amount of each ingredient is used, which is crucial for achieving the desired concrete quality.
3. Mixing Unit
The mixing unit is where all components are combined. Depending on the design and requirements, this can be a drum, pan, or twin-shaft mixer.
4. Control Systems
Modern batching plants are equipped with sophisticated control systems that allow for precise monitoring and management of the entire batching process, increasing efficiency and output reliability.
Applications of Concrete Batching Plants
Concrete batching plants serve various applications across the construction sector:
- Infrastructure Projects: Roads, bridges, and airports greatly benefit from the efficient concrete supply.
- Commercial Buildings: High-rise buildings and commercial complexes require large volumes of concrete, making batching plants indispensable.
- Residential Housing: From single-family homes to multi-story apartments, batching plants support residential construction.
- Precast Concrete Production: Many plants also serve the precast industry, producing components off-site before final assembly on construction sites.
The Future of Concrete Batching Plants
As technology evolves, so too do concrete batching plants. The future holds promising advancements, including:
- Automation: Increased use of automated processes will further streamline production and reduce costs.
- Smart Technology: IoT (Internet of Things) capabilities will enable real-time monitoring and diagnostics, improving operational efficiencies.
- Sustainability: Innovations aimed at recycling and reducing waste will make batching plants more environmentally friendly, contributing to sustainable construction practices.
Conclusion
Concrete batching plants are indispensable in today’s construction landscape, providing efficiency, flexibility, and superior quality in concrete production. With numerous types catering to varied demands, these facilities are the backbone of infrastructure development, paving the way for the cities of tomorrow. Embracing the advancements in technology and sustainable practices will ensure that concrete batching remains a critical player in the construction industry. Explore more about concrete batching plants and their innovations at Polygonmach.