Transforming Industries: A Comprehensive Guide to China Plastic Mould Factory
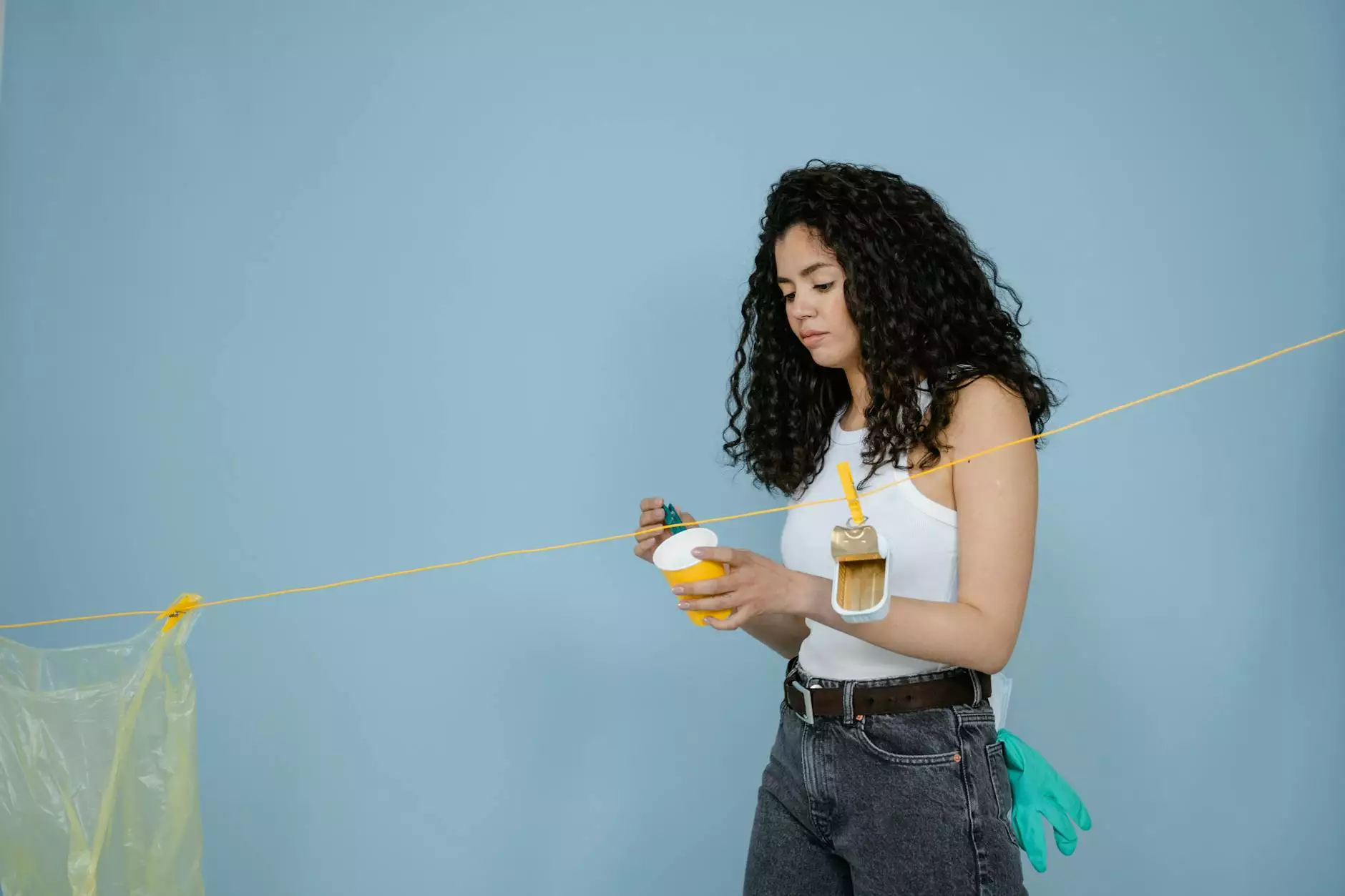
The rapid advancement of technology and growing consumer demands have led to an unprecedented evolution in manufacturing processes, especially in the plastic industry. In this dynamic environment, the significance of a China plastic mould factory cannot be overstated. A reputable company in this field, such as Hanking Mold, exemplifies how precision engineering, innovative design, and exceptional craftsmanship can drive economic growth and facilitate advancements across multiple sectors.
Understanding the Role of a Plastic Mould Factory
Plastic mould factories are crucial players in the manufacturing ecosystem. They specialize in creating molds that enable the production of plastic components used in countless products. Without these specialized factories, the production lines of industries such as automotive, electronics, consumer goods, and healthcare would face significant bottlenecks.
What is a Plastic Mold?
A plastic mold is a hollowed-out block that is used to obtain a desired shape through a manufacturing process known as injection molding. This process involves injecting molten plastic materials into the mold, where it cools and solidifies to form an object. The precision and quality of these molds directly influence the performance and characteristics of the final product.
Key Advantages of Working with a China Plastic Mould Factory
Partnering with a China plastic mould factory like Hanking Mold presents numerous advantages that can significantly impact business operations and product quality. Below are some key benefits:
- Cost-Effectiveness: Manufacturing costs in China are often lower due to reduced labor and material expenses. This cost advantage can be leveraged by companies looking to optimize their budgets.
- Expertise and Experience: Established factories bring decades of experience in mold design and manufacturing, ensuring high-quality outputs that meet international standards.
- Advanced Technology: Many Chinese mold factories employ cutting-edge technology and innovative practices that enhance precision, durability, and efficiency.
- Flexible Production Volume: Whether a business requires a small batch production or large-scale manufacturing, these factories can accommodate various needs with agility.
- Rapid Turnaround Times: Recognizing the need for speed in today’s markets, leading factories like Hanking Mold offer quick production times to meet tight deadlines.
Top Services Offered by Hanking Mold
As a prominent plastic injection mould manufacturer, Hanking Mold offers a broad range of services tailored to meet diverse industry requirements. Some of these services include:
1. Custom Mold Design
At Hanking Mold, the journey begins with understanding a client’s needs. Our talented engineers work closely with clients to develop custom mold designs that optimize functionality and manufacturability.
2. Injection Molding
Utilizing state-of-the-art machinery, we provide efficient and consistent injection molding services. Our advanced techniques ensure that every component exhibits the highest quality standards, meeting the precise specifications of our clients.
3. Prototype Development
Before mass production, we assist clients with creating prototypes. This critical step allows businesses to test and refine their designs, ensuring the final product meets expectations.
4. Mold Maintenance and Repair
To extend the lifespan of molds and ensure optimal performance, Hanking Mold provides comprehensive maintenance and repair services. This proactive approach reduces downtime and improves overall production efficiency.
5. Material Selection Support
Choosing the right plastic material is crucial for product integrity and performance. Our team offers expertise in material selection, helping clients decide on materials that align with their product goals and standards.
The Process of Plastic Injection Molding in China
The plastic injection molding process at Hanking Mold can be segmented into several critical stages. Understanding this process can provide insight into how we maintain quality and efficiency throughout production:
Stage 1: Design and Engineering
The first stage involves creating detailed mold designs. Our engineers utilize advanced CAD software to design molds that are complex yet functional. This stage includes thorough discussions with clients to finalize the design concepts.
Stage 2: Prototype Development
Next, prototypes are produced to assess the design's feasibility. This allows for adjustments to be made before the final mold is manufactured, saving time and resources.
Stage 3: Mold Production
Once the prototype is approved, we move to mold production. High-grade steel is commonly used for molds, ensuring they withstand high-pressure injections and repeated use without degrading.
Stage 4: Injection Molding
At this stage, preheated plastic resin is injected into the mold under high pressure. After cooling, the mold opens, allowing the finished part to be ejected. Quality checks are performed at this stage to ensure every component meets the required specifications.
Stage 5: Finishing and Assembly
After injection molding, parts may require additional finishing processes such as trimming, polishing, or assembly. Hanking Mold provides these services to deliver ready-to-use components.
Environmental Responsibility in Plastic Moulding
As industries worldwide face increasing scrutiny regarding environmental impact, Hanking Mold remains committed to sustainable practices in the plastic moulding sector. Our factory implements several eco-friendly strategies:
- Recycling Materials: We prioritize the use of recyclable materials and encourage clients to consider sustainable options during the design phase.
- Waste Reduction: Through efficient production processes, we minimize waste, ensuring as little material as possible goes unused.
- Energy Efficiency: Investing in energy-efficient machinery and practices contributes to lower carbon footprints and reduces operating costs.
Choosing the Right China Plastic Mould Factory
When selecting a plastic mould factory, it is crucial to consider several factors that ensure you make an informed choice. Hanking Mold embodies these qualities, making us a preferred choice for many businesses:
1. Quality Assurance
Quality assurance processes are essential in the production of molds and components. Hanking Mold employs rigorous testing protocols to ensure that every product is delivered to the highest standards.
2. Customer Support
Maintaining open lines of communication with clients is vital. We provide exceptional customer support throughout the project lifecycle, addressing concerns and providing updates.
3. Industry Expertise
Our team’s extensive experience in various industries enables us to understand unique challenges and requirements, offering tailored solutions that drive results.
4. Technology and Innovation
Staying up-to-date with the latest technology is critical in today’s fast-paced market. Hanking Mold continually invests in innovation to improve our services and offerings.
Conclusion: The Future of Plastic Mold Manufacturing in China
The future of manufacturing in China, particularly in the realm of plastic moulding, looks promising. With continuous advancements in technology, growing expertise, and a commitment to sustainability, factories like Hanking Mold are set to lead the charge in revolutionizing the industry.
By choosing a reliable plastic injection mould manufacturer like Hanking Mold, companies not only gain access to premium-quality products but also enjoy the peace of mind that comes from working with a dedicated team that prioritizes client success. As we move forward, the potential for growth and innovation within the China plastic mould factory sector will only expand, presenting countless opportunities for collaboration and progress.
For businesses looking to elevate their production capabilities, collaborating with a trusted partner such as Hanking Mold is the way forward. Reach out to us today to learn how we can assist you in achieving your production goals.