CNC Lathing Parts: Precision and Efficiency in Metal Fabrication
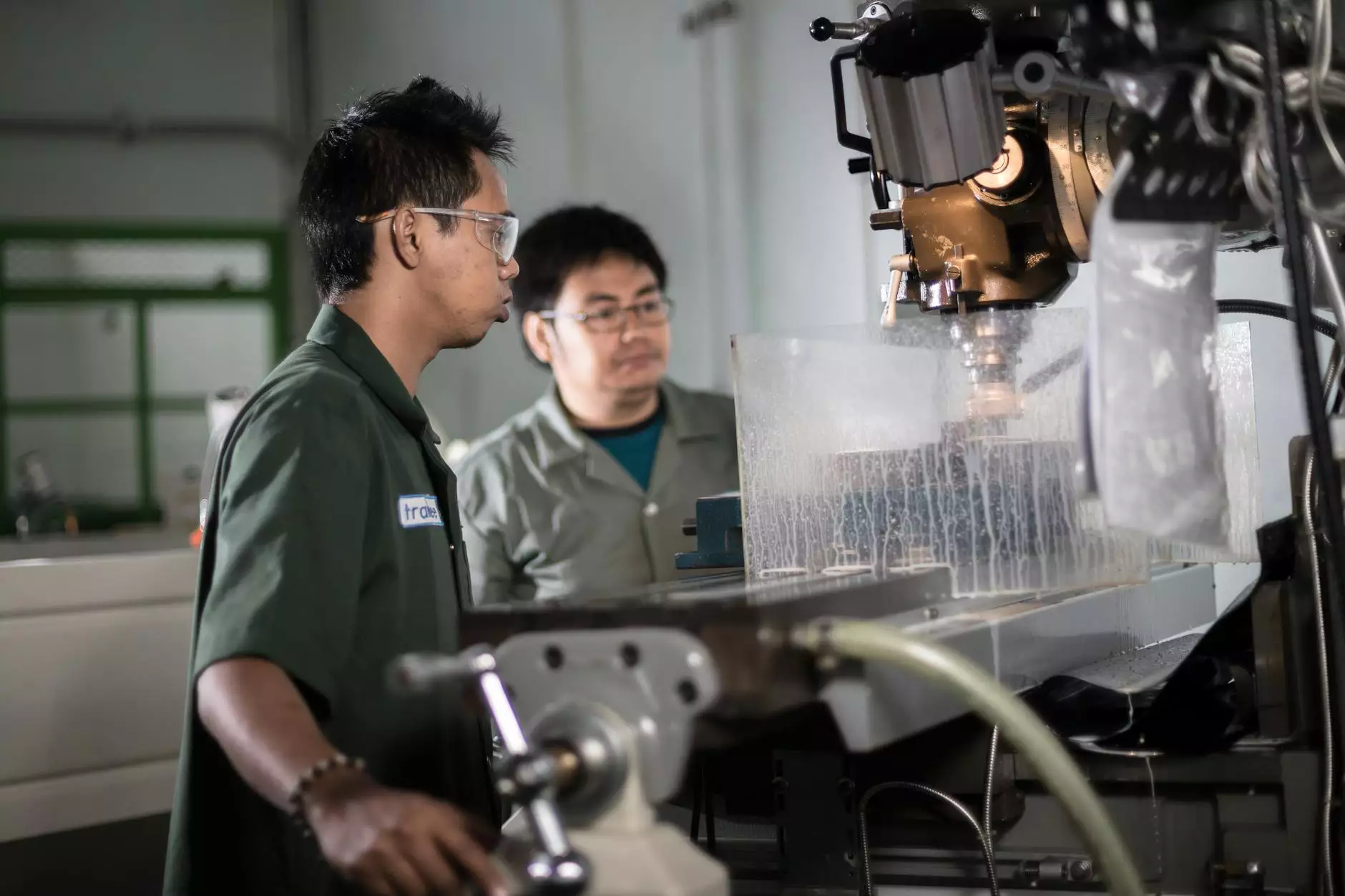
CNC lathing parts are integral to the manufacturing process, playing a critical role in creating precise components across a wide array of industries. From automotive to aerospace, the demand for high-quality, tailored parts continues to grow. Understanding the significance of these components and how they are produced is essential for businesses looking to optimize their production capabilities.
What are CNC Lathing Parts?
CNC lathing parts are components made using CNC (Computer Numerical Control) lathes, a sophisticated type of machinery that shapes materials through the removal of excess material from a rotating workpiece. This process is exceptionally efficient, allowing for high precision and repeatability, making it a preferred choice for manufacturers globally.
How Does CNC Lathing Work?
At the core of CNC lathing is the ability of the machine to carry out programmed cuts and designs automatically. The basic steps involved in manufacturing cnc lathing parts include:
- Design: Create a 3D model of the part using CAD (Computer-Aided Design) software.
- Programming: Convert the CAD model into CNC machine code, determining how the machine will move and operate.
- Material Setup: Secure the raw material, usually metal, plastic, or composite, in the lathe.
- Machining: Execute the programmed instructions, where the lathe rotates the material while tools cut away the excess.
- Finishing: Apply processes like polishing or anodizing to create the final finish and specifications required.
The Advantages of CNC Lathing Parts
Utilizing cnc lathing parts offers numerous benefits that enhance manufacturing efficiency and product quality:
1. Precision and Consistency
CNC lathes provide unparalleled precision in manufacturing, producing parts that conform to tight tolerances. This consistency is crucial for parts that must fit together perfectly in assemblies.
2. Versatility of Materials
With the capability to work with a variety of materials—including metals such as steel, aluminum, and brass—CNC lathing can cater to different industry requirements.
3. Reduced Labor Costs
Automating the lathing process minimizes manual labor, which can lead to cost savings and higher output levels.
4. Enhanced Production Speed
Thanks to the efficiency of CNC operations, parts can be produced quicker than traditional methods, allowing businesses to meet deadlines without compromising quality.
Applications of CNC Lathing Parts
CNC lathing parts are used in various sectors due to their precision and adaptability. Here are some common applications:
- Aerospace: Critical components for aircraft engines and structural parts.
- Automotive: Engine components, transmission parts, and fittings that require high durability.
- Medical: Instruments and implants that necessitate high precision and compliance with regulations.
- Electronics: Enclosures and housings for devices often need bespoke parts to accommodate specific designs.
Turning to DeepMould.net for CNC Lathing Parts
As a player in the realm of metal fabricators, DeepMould.net sets itself apart through a commitment to quality and customer satisfaction. Here’s why choosing us for your CNC lathing needs makes sense:
Quality Assurance
At DeepMould.net, quality is non-negotiable. Each cnc lathing part undergoes rigorous quality checks to ensure compliance with industry standards. Our advanced quality management system guarantees that every part meets or exceeds client specifications.
Cutting-Edge Technology
We leverage the latest in CNC machinery technology, allowing us to deliver intricate designs and specifications. Our equipment is continually upgraded to maximize efficiency and output quality.
Expertise and Experience
Our team of specialists brings years of experience and technical know-how to the table. This expertise ensures that we can tackle even the most complex projects, providing tailored solutions to meet specific industrial demands.
Rapid Prototyping Capabilities
Need a part quickly? DeepMould.net offers rapid prototyping services that expedite the design and manufacturing process. This agility allows clients to see their designs come to life without unnecessary delays.
The Future of CNC Lathing in Metal Fabricators
The future of cnc lathing parts is bright, with advancements in technology continuing to drive innovation in the field of metal fabrication. As industries evolve, the need for more precise, efficient, and customizable parts will only increase.
Emerging Trends in CNC Technology
Some of the current trends that are shaping the future of CNC lathing include:
- Automation and Robotics: Increasing installation of robotics in CNC operations to enhance speed and accuracy.
- IoT Integration: The use of Internet of Things (IoT) technology for better data collection and monitoring of manufacturing processes.
- 3D Printing Synergies: The combination of CNC machining with 3D printing technologies can enhance production capabilities.
- Sustainability Techniques: Adoption of eco-friendly practices to minimize waste and improve energy efficiency within machining processes.
Conclusion
In an era where precision, efficiency, and quality are paramount, the role of cnc lathing parts cannot be overstated. They form the backbone of numerous industries, and choosing a reliable manufacturer like DeepMould.net ensures that businesses can maintain their competitive edge. Through a combination of cutting-edge technology, quality assurance, and expert knowledge, we are committed to delivering outstanding CNC lathing solutions that meet and exceed our clients' expectations.
Explore our range of cnc lathing parts today and discover how DeepMould.net can support your business with precision metal fabrication that goes above and beyond.