Plastic Injection Mold Makers: Revolutionizing Manufacturing
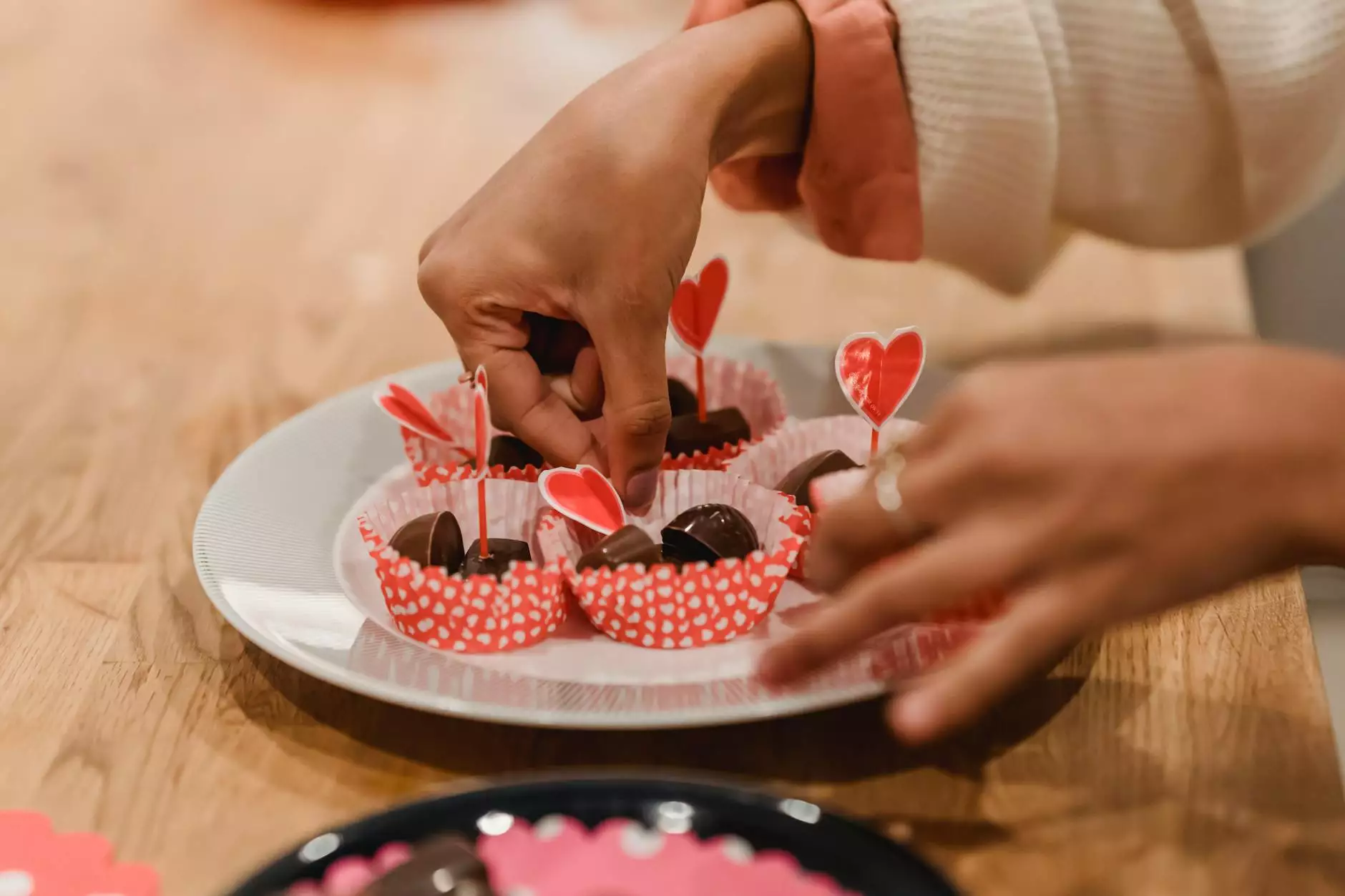
In today’s fast-paced industrial landscape, the need for high-quality, efficient manufacturing processes has never been greater. One of the most critical components in achieving this efficiency is the role of plastic injection mold makers. These artisans and engineers craft the molds that form the very foundation of countless products we use daily. This article delves deep into the intricacies of this industry and highlights how businesses can leverage mold-making capabilities to enhance their operations. We will explore topics such as the design process, materials used, and the technological advancements that are shaping the future.
Understanding Plastic Injection Molding
Plastic injection molding is one of the most widely utilized manufacturing processes in the production of plastic parts. It involves the injection of molten plastic into a mold, where it cools and solidifies into the desired shape. This technique offers several advantages:
- High Efficiency: The cycle time for injection molding is significantly shorter than many other processes, allowing for rapid production.
- Cost-Effectiveness: Once the initial mold is made, the cost per part decreases dramatically with large production runs.
- Consistency: Injection molding guarantees uniformity in parts, making it an excellent choice for mass production.
- Versatility: A wide range of materials can be used, including various thermoplastics and thermosetting polymers.
The Role of Plastic Injection Mold Makers
Plastic injection mold makers are essential players in this process. They not only create the molds but also optimize them for efficiency and durability. Their work involves several stages, from initial concept design to final production. Here’s a brief overview of their roles:
1. Design and Prototyping
Before a mold can be created, it must first be designed. Mold makers use advanced software to create 3D models that simulate the final product. This phase includes:
- Consultation with Clients: Understanding the specifications and requirements of the product.
- Software Modeling: Using CAD (Computer-Aided Design) software to create detailed models.
- Prototyping: Building prototypes to test the design before production.
2. Material Selection
The choice of materials for mold making is critical. Mold makers must select materials that provide durability and precision. Some common materials include:
- Steel: Ideal for high-volume production due to its strength and resistance to wear.
- Aluminum: Suitable for lower volume production and offers shorter lead times.
- Composites: Emerging materials that combine strength with reduced weight.
3. Tooling and Manufacture
Once the design and materials are settled, molds are fabricated through various manufacturing processes:
- CNC Machining: Computer-controlled machinery is used to create precise mold components.
- EDM (Electrical Discharge Machining): This process is crucial for intricate designs that require high accuracy.
- 3D Printing: Rapid prototyping techniques are becoming increasingly popular for creating molds.
Quality Assurance in Mold Making
Quality assurance is paramount in the work of plastic injection mold makers. A well-made mold not only produces high-quality parts but also minimizes waste and defects. Key aspects of quality assurance include:
- Regular Inspections: Continuous monitoring of the mold production process is vital to ensure adherence to specifications.
- Testing Procedures: Molds are tested for performance using sample runs to detect any potential issues.
- Feedback Loops: Continuous improvement processes based on client feedback help in refining mold production.
The Impact of Technology on Plastic Injection Molding
Technological advancements are significantly shaping the landscape of plastic injection mold makers. Some notable innovations include:
1. Automation
Automation in the injection molding process has led to enhanced efficiency and precision. With automation, consistency in production is easily achievable, reducing human error.
2. Advanced Software Solutions
Modern mold makers leverage sophisticated software for simulation and design, allowing for better prediction of how materials will flow during the injection phase, reducing issues before production starts.
3. Sustainable Practices
There is a growing trend towards sustainability in the plastic industry. Mold makers are now using eco-friendly materials and processes to minimize their environmental impact. This shift not only meets consumer expectations but also drives down costs by reducing material waste.
Choosing the Right Plastic Injection Mold Maker
For businesses looking to outsource their mold-making needs, choosing the right partner is crucial. Here are some key factors to consider:
- Experience and Expertise: Look for mold makers with a proven track record in your specific industry.
- Technology and Equipment: Advanced machinery and technologies can significantly affect the quality of the molds produced.
- Communication: A responsive and communicative partner can help streamline the process and ensure that your needs are met.
- Cost vs. Quality: While cost is an important factor, it should not compromise quality. Choose a mold maker that offers the best balance between the two.
Conclusion: The Future of Plastic Injection Mold Making
The landscape of plastic injection mold makers is poised for exciting growth and transformation. As technological advancements continue to evolve, these mold makers will become even more integral to manufacturing. Their capabilities can drive innovation, enhance product quality, and significantly improve operational efficiency. For businesses, understanding the importance of collaboration with skilled mold makers is essential to staying competitive in an ever-changing market.
At DeepMould.net, we understand the challenges faced by manufacturers and are dedicated to providing top-notch services in mold making and metal fabrication. By partnering with seasoned professionals who prioritize quality and innovation, businesses can unlock their full potential and meet the demands of today’s consumers while paving the way for a sustainable future.